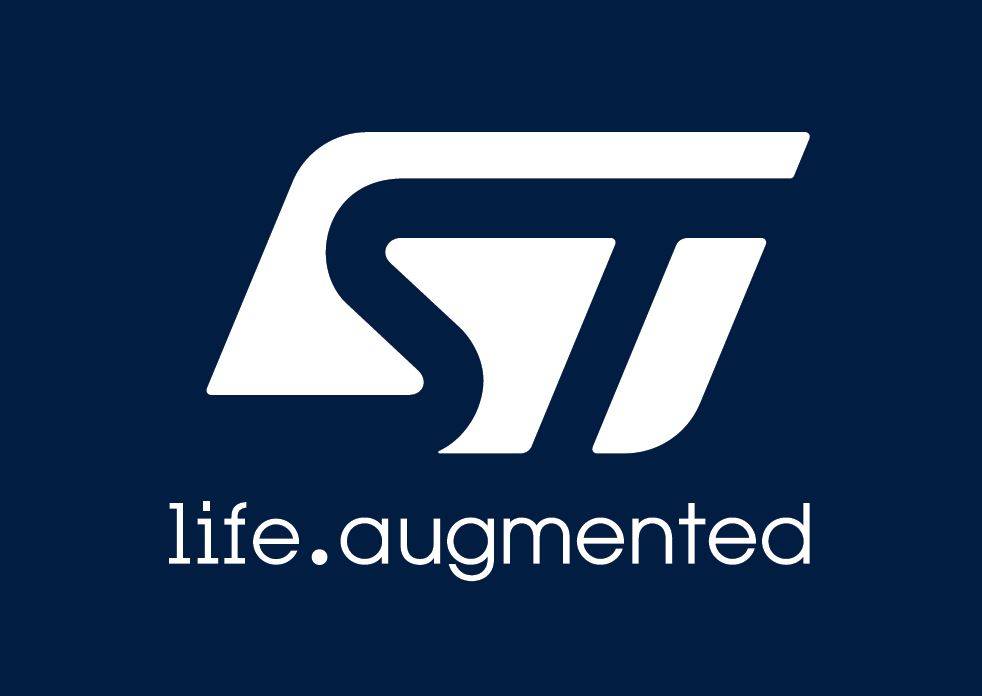
STMicroelectronics has released STM32ZeST(Zero speed Full torque) software algorithm. The algorithm, which runs on the STM32 microcontroller, enables the non-inductive motor drive to generate maximum torque at zero RPM. Italian-french Semiconductor is currently sharing this algorithm with selected customers. This algorithm provides zero speed full torque motor control function for the first time in general-purpose motor drivers, and realizes the motor running smoothness and predictability that could not be achieved before.
Power tools, electric curtains, washing machines, automatic lawn mowers, air conditioning systems, electric bicycles and other product equipment require the motor to start in the correct direction with maximum torque and/or maximum load to start quickly, while consuming minimal electrical energy. Ordinary non-inductive motor drivers cannot determine the rotor position of the motor at zero speed and, therefore, cannot meet the requirements of these devices. Previously, to ensure accurate positioning, high energy efficiency and correct operation, it was often necessary to add hardware position sensors or use special types of motors.
The new STM32ZeST software algorithm is a zero-speed non-inductive motor control optimization universal solution that supports any type of permanent magnet synchronous motor (PMSM). In order to achieve optimal control, the STM32ZeST algorithm needs to run synchronously with the newly introduced High Sensitivity Observer (HSO) algorithm, using a sensorless non-inductive mode to control the motor operation. As an embedded software solution, no additional hardware or special peripherals are required on the STM32 microcontroller (MCU). To ensure that motor control remains energy efficient, the resistance of the motor is also estimated at runtime.
By using STM32ZeST and HSO software algorithms, designers can avoid peak currents during the start-up phase and improve the energy efficiency of the application. Compared to motor drives with Hall sensors, ST's solutions reduce the cost of material (BOM), improve operational reliability, and reduce noise. St has developed a demonstration model that shows how a non-inductive motor drive can start, moving the load at a variety of RPM and minimum RPM. The model uses a wheel with an electric pedal to demonstrate that the motor always starts in a predetermined direction and can keep the load stationary at zero speed.
In order to facilitate developers to evaluate the performance of STM32ZeST and HSO algorithms and speed up the development process, ST has developed supporting hardware tools, among which the B-G473E-ZEST1S control board generates PWM signals for the power board STEVAL-LVLP01. The power strip drives low-power/low-voltage motors, such as those in ST's B-MOTOR-PMSMA suite. The control board is connected to the power board using the new embedded motor control connector V2.
ST provides developers with a number of additional support services to help them develop drives for popular motor types that meet a variety of application needs and meet energy efficiency, size, performance and cost constraints. The STM32 series of microcontrollers can meet a variety of performance requirements, many products integrate features suitable for motor control, for example, advanced motor control PWM timer, the ST Motor Control Software Development Kit (MC-SDK) supports all of these products, The kit includes a Motor Control firmware library and a dedicated configuration tool (Motor Control Workbench). Both tools need to work with the STM32Cube ecosystem and the STM32CubeMX project configurator.
The HSO algorithm is integrated in the new MCSDK(version 6.2) development kit. The new MCSDK adds a dual-drive solution that runs on STM32 G4 MCUS and also supports a wide range of STM32 microcontrollers from the cost-effective STM32C0 to the high-performance STM32H5.
The Products You May Be Interested In
![]() |
AMI-27B-12-3 | LINE FILTER 250VAC 12A CHASS MNT | 322 More on Order |
![]() |
AMI-29B-16-3 | LINE FILTER 110/250VAC 16A CHAS | 350 More on Order |
![]() |
AMI-M11H-1-4-A | LINE FILTER 250VAC 4A CHASS MNT | 144 More on Order |
![]() |
AMI-M11P-6-20-B | LINE FILTER 250VAC 6A CHASS MNT | 353 More on Order |
![]() |
AMI-M11O-6-30-B | LINE FILTER 250VAC 6A CHASS MNT | 407 More on Order |
![]() |
AMI-23-12-3 | LINE FILTER 250VAC 12A CHASS MNT | 193 More on Order |
![]() |
AMI-M11P-3-6-B-2 | LINE FILTER 250VAC 3A CHASS MNT | 320 More on Order |
![]() |
AMI-M12Q-1-6-B | LINE FILTER 250VAC 6A CHASS MNT | 313 More on Order |
![]() |
AMI-23A-6-3 | LINE FILTER 250VAC 6A CHASS MNT | 136 More on Order |
![]() |
AMI-23B-4-3 | LINE FILTER 250VAC 4A CHASS MNT | 154 More on Order |
![]() |
AMI-22B-3-3 | LINE FILTER 250VAC 3A CHASS MNT | 412 More on Order |
![]() |
AMI-M11D-3-10-B-2 | LINE FILTER 250VAC 3A CHASS MNT | 498 More on Order |
![]() |
AMI-21A-1-3 | LINE FILTER 250VAC 1A CHASSIS | 488 More on Order |
![]() |
AMI-M11UC-1-16-C | LINE FILTER 250VAC 1A CHASS MNT | 102 More on Order |
![]() |
AMI-M12B-1-20-B | LINE FILTER 250VAC 20A CHASS MNT | 272 More on Order |
![]() |
AMI-22A-20-1 | LINE FILTER 250VAC 20A CHASS MNT | 458 More on Order |
![]() |
AMI-M11R-7-10-B-1 | LINE FILTER 250VAC 10A CHASS MNT | 340 More on Order |
![]() |
AMI-M11D-6-20-B-1 | LINE FILTER 250VAC 20A CHASS MNT | 147 More on Order |
![]() |
AMI-M12A-6-10-B | LINE FILTER 250VAC 10A CHASS MNT | 198 More on Order |
![]() |
AMI-M11R-7-6-B-2 | LINE FILTER 250VAC 6A CHASS MNT | 334 More on Order |
![]() |
AMI-23-6-1 | LINE FILTER 250VAC 6A CHASS MNT | 422 More on Order |
![]() |
AMI-22-3-3 | LINE FILTER 250VAC 3A CHASS MNT | 157 More on Order |
![]() |
AMI-M11A-1-10-D | LINE FILTER 250VAC 10A CHASS MNT | 375 More on Order |
![]() |
AMI-21B-1-1 | LINE FILTER 250VAC 1A CHASS MNT | 250 More on Order |